The role of smart technologies in improving solar project costs and yields in India. Sunil Jain is the CEO and Executive Director of Hero Future Energies (HFE), an independent power producer that has an installed capacity of 1.2 GW and is striving to cross 3.5 GW by 2022.
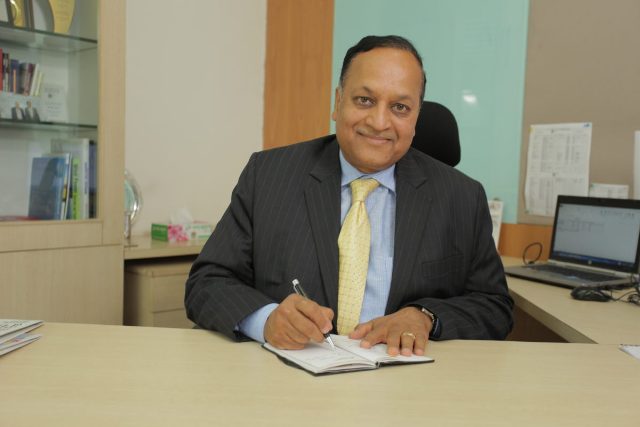
Hero Future Energies
As India’s leading independent power producer with an established global presence, what are your continued plans for growing renewable energy over the next three years?
Hero is presently operating approximately 1,500 MW of wind and solar assets, and has around 1,000 MW under construction, with another 1,000 MW under development. We plan to reach a capacity of 5 GW of solar in the next three to four years. Hero will also go for a lot of innovative projects, like hybrid or tribrid with wind and storage in the coming years.
How would you describe the evolution of India’s energy sector thus far?
The Indian energy sector continues to grow at 6-7% annually. It is evolving to include a large mix of renewable energy and also adopting new technologies to get 30% renewables onto the grid by 2022. I believe then that our energy sector will gradually move to low carbon as renewables will become mainstream in the energy mix.
What role are cutting-edge digital technologies, such as machine-to-machine learning and Internet of Things (IoT), playing in this evolution?
Huge! There are three stages of solar and wind power plants: design, execution, and operation. At the design stage, the use of drones, in conjunction with differential GPS, for land-based topography with artificial intelligence is immensely helpful in plant layout design, drainage design, earth-work assessment, etc. This is creating much more accuracy and speed.
At the execution stage, piling and ramming using GPS-based machines ensure automated location of pile coordinates. Even drone-based plant monitoring and process data generation through AI and machine learning is possible. At the operation stage, state-of-the-art robotic cleaning systems, mounted with wind sensors, pyranometers, and IoT-based data analytics, can govern the smart cleaning of modules to ensure higher [power] generation.
The use of drones laded with thermal camera and GPS enables perfect monitoring of module behavior, and defects are diagnosed through machine learning and AI-based data analytics. With string-level monitoring features, it is now possible to communicate string data through IoT, leading to error-free data for accurate assessment. With multi-MPPT (maximum power point tracking) string inverters using high-end algorithms, it is possible to assess the behavior of each string, including the I-V curve. This can effectively prevent technical issues, improve O&M efficiency, and reduce O&M costs.
Power electronics can be the cause of failures in solar installations. In India, what are the specific requirements that inverters must meet?
Reliability and performance of power electronics-based devices are critically dependent on the ambient temperature, humidity, and presence of vermin, etc. Tropical countries like India are characterized by high temperatures and levels of humidity, and also have the presence of lizards, rodents, and snakes. The inverters must be designed to have protection from such extremes.
What made you choose Huawei as your preferred inverter partner?
Huawei is one of the largest R&D-oriented organizations, with their products using state-of-the-art technology. The company manufactures high-efficiency string inverters, with greater than 99% efficiency and the multi-MPPT feature, unlike central inverters which carry efficiencies of approximately 98.3% and single MPPT. Multi-MPPT is extremely advantageous for installing PV systems on any land profile, including high sand dunes or mountainous zones. Due to Huawei’s high-end technology, it is possible to load such inverters beyond 200% DC. There is an observable gain of more than 3% vis-à-vis central inverters. With the inverters being distributed in nature, their mean time to repair is also very low.
Does the thinning of profit margins due to falling tariffs mean compromises on the quality of the projects?
The solar PV sector has gone through an immense innovation phase and a great learning curve. Initially, the balance of system design was drawn in equivalence with thermal plants, which run at 100% capacity, 24/7. Designers have gradually unlearned that, and adapted to the behavior of solar PV plants. This has led to innovations and optimizations without compromising quality.
For large-scale PV plants, better data analytics and smart monitoring of the plant are possible, which can ensure better preemptive maintenance and improved generation. Tariffs have fallen due to the aforementioned points, and the immense price reductions in modules. It is therefore believed that there need be no compromise in the quality.
How can O&M costs be minimized over the life cycle of a project?
More and more usage of smart technologies such as robotic cleaning, soiling loss measurement kits, drone-based thermography, smart inferences through machine learning from SCADA data analytics, automated grass-cutting machines, and inverter and transformer health diagnostics through machine learning can minimize O&M costs without any compromise, and even with better generation.
From: PV Magazine Huawei Special